- Новости
- Евгений Васильев: «В феврале – марте, думаю, мы начнем выпускать первые партии титановых имплантатов»
Евгений Васильев: «В феврале – марте, думаю, мы начнем выпускать первые партии титановых имплантатов»
30.12.2016
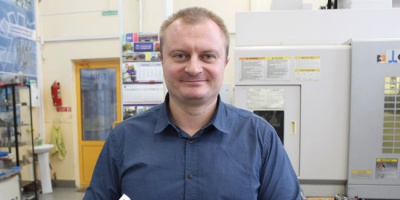
Он используется в наиболее важных отраслях – авиа– и ракетостроении, промышленности, а также в медицине. В частности, титановые сплавы широко применяют для создания имплантатов. Именно о таком производстве корреспонденту «КВ» Анастасии ИЛЬЧЕНКО рассказали профессор Андрей ПОПОВ и доцент кафедры «Металлорежущие станки и инструменты» ОмГТУ Евгений ВАСИЛЬЕВ, которые занимаются созданием производства титановых имплантатов.
– Андрей Юрьевич, что представляет собой производство титановых имплантатов?
Андрей ПОПОВ.
Есть три основные технологии: 3D-прототипирование, фрезерование из прутка и листовая штамповка. Первая позволяет сделать любую форму имплантата, но отличается невысокой прочностью. Фрезерование дает прочное и универсальное изделие, но очень дорого обходится станок, инструмент, и много металла идет в стружку. А титан стоит порядка 3 тысяч рублей за килограмм. Наша технология, которая вышла из недр нашей промышленности, – штамповка из листа. Из него на специальной установке вырезаются плоские заготовки, а потом на горячем штампе изгибаются. В итоге получаются изделия прочнее и дешевле, чем за рубежом.
– Для создания имплантатов нужно специальное оборудование?
ПОПОВ. Оборудование для них требуется в основном универсальное, поэтому мы используем возможности ОмГТУ – интеллектуальные и физические. Например, оборудование, на котором можно делать пазы, резьбы. У нас есть кафедра «Теория и обработка металлов давлением», специалисты которой могут спроектировать штамп, есть участок механической обработки со станками, где можно делать имплантаты, есть 3D-сканеры, принтеры, чтобы сделать чертеж.
Евгений ВАСИЛЬЕВ. Изготавливаем также титановые саморезы. Все детали в обязательном порядке маркируются лазером, который купил университет. Конечно, это многоцелевое оборудование, на нем можно маркировать все что угодно, делать значки, медали. Сейчас покупается нагревательная печь, «барабан», чтобы снимать окалину, оснастка для гибочного пресса.
– Вы подсчитывали, сколько оборудования закуплено специально для производства имплантатов?
ПОПОВ. Примерно на 6 млн рублей. Но чтобы получить их, нужно было сделать хотя бы один штамп и убедить руководство университета в реальности получения прибыли и наличии спроса. От идеи до реализации прошел почти год. – В России кто-нибудь еще выпускает титановые имплантаты? ПОПОВ. У нас мало качественного отечественного товара в этой сфере. Импортные имплантаты предизогнутые, сделаны по форме кости, а отечественные – прямые, сделаны под технологию. Есть крупное производство в Пензе, где используют технологии штамповки простых изделий. Но у них хромает качество головки шурупов. Представьте только, что головки срываются, и хирург вынужден проводить в кости человека слесарную операцию. Поэтому врачи предпочитают импортные образцы, вплоть до того, что люди сами покупают их, чтобы операция прошла нормально. Мы сейчас разрабатываем технологию их изготовления и уже научились делать головку идеально. Наш инженер Владимир Александрович БУШЕВ занимается размещением заказа на изготовление этого шурупа из титанового сплава. Он долгое время работал заместителем главного инженера на заводе им. Баранова и занимался вопросами изготовления штампов. Его производственный опыт и позволил нам выйти на эту технологию, организовать производство.
– Форма, повторяющая физиологический изгиб кости, – это ваше изобретение?
ВАСИЛЬЕВ. Мы переняли импортные аналоги. Они отработали их, разбили на градации, и мы пришли на готовое. Дело в том, что форму запатентовать нельзя, их выпускает огромное количество фирм.
– Как возникла идея изготовления титановых имплантатов в ОмГТУ?
ВАСИЛЬЕВ. Она пришла от хирургов МСЧ-10. У них идут массовые операции по установке имплантатов, и они предложили организовать это производство у нас. Есть порядка 20 ходовых типоразмеров имплантатов – для голени, ключицы, предплечья, шейки бедра, они перекрывают 90 процентов всех переломов, а все остальные случаи требуют индивидуальных доработок. С помощью имплантатов человек уже через несколько дней может ходить, а раньше с переломом шейки бедра лежал месяцами. С применением имплантатов смертность резко снизилась.
ПОПОВ. Индивидуальные имплантаты мы можем делать по традиционной технологии, без штампа. Хирурги нам задают вопросы, например, как сделать титано-силиконовые имплантаты. Какой-то неадекватный человек выстрелил женщине в грудь, и теперь хирурги не могут жестко закрепить ребра, потому что человеку будет неудобно двигаться и дышать, требуется создать подвижность. Конечно, индивидуальных имплантатов нужно немного, но все случаи их использования трагические и требуют быстрого реагирования. С зарубежными изделиями работать сложнее: сначала 3D-модель отправить туда, потом ждать, пока изготовят, вышлют. Это может длиться месяцами, и иногда бывает уже поздно.
– На какой стадии сейчас организация нового производства?
ВАСИЛЬЕВ. Идет лицензирование. Чтобы начать производство, много времени не требуется, буквально в феврале – марте, думаю, мы начнем выпускать первые партии титановых имплантатов и реализовывать их компаниям, у которых есть право на продажу подобной продукции.
– Каким образом вы собираетесь их реализовывать?
ВАСИЛЬЕВ. Сами торговлей заниматься не будем. Свяжемся с торговыми фирмами, сделаем им большую скидку. Можем работать на склад, где постоянно будет лежать запас имплантатов. Получить их оттуда можно гораздо оперативнее, чем из-за рубежа.
– Какие планируются объемы производства?
ПОПОВ. Хотим выйти на 10 – 15 тысяч штук в год. В Омске ежегодно имплантатов требуется порядка 10 тысяч. Все типы сразу мы не сможем освоить. У нас есть интересанты в Омске, Новосибирске, Казахстане, но у них одна беда – нет склада. А он необходим, стоимость одного изделия очень высока. Американский имплантат стоит 70 тысяч рублей, а корейский – 40.
– А ваш?
ПОПОВ. Примерно 20 тысяч рублей. Мы полагаем, что нам удастся сделать такие же качественные имплантаты, как американские, и в четыре раза дешевле. Дальше, думаю, у нас рынок будет расширяться геометрически. Да, конкуренция предстоит жесткая: американцы под Москвой имеют завод, а корейцы строят во Владивостоке. Но мы по цене сможем опускаться ниже, чем они смогут себе позволить. У нас более дешевая технология. А если они захотят нас «раздавить», то населению России будет только хорошо. Если начнут демпинговать – люди будут покупать имплантаты в несколько раз дешевле, чем сейчас.
– Сколько людей на проекте задействовано сейчас и сколько будет, когда начнется производство?
ВАСИЛЬЕВ. Сейчас шесть – это разработчики. Потом будет 10 – 15. Производством займутся студенты: в свободное от учебы время будут зарабатывать деньги.
– Евгений Владимирович, что вам ближе – научная работа или производственная деятельность?
ВАСИЛЬЕВ. Иногда хочется отвлечься от работы на компьютере и что-то выточить на станке, а иногда, наоборот, тянет подумать.
ПОПОВ. Университет дает возможность преподавателям зарабатывать. У нас на кафедре в год хоздоговоров НИИР заключается на 30 – 40 млн рублей. Четверо ассистентов, которые работают на 0,5 и 0,25 ставки, – специалисты экстра-класса по наладке и программированию на станках с ЧПУ, они обучают студентов, а когда нет занятий, работают на станках. Зарплата у них выходит в несколько раз выше, чем у квалифицированных преподавателей: за счет преподавания – копейки, в основном за продукцию и подготовку кадров операторов, наладчиков, инженеров-программистов станков с ЧПУ для омских предприятий.
– Евгений Владимирович, у вас много патентов?
ВАСИЛЬЕВ: – В соавторстве за последние десять лет у нас появилось около 13 патентов. Один на изобретение, остальные на полезные модели – станки, инструменты.
– А остается время на хобби?
ВАСИЛЬЕВ. Несколько раз в год, когда приезжаю к родителям в Тарский район, хожу на рыбалку. Занимаюсь волейболом, в ОмГТУ есть своя команда, мы участвуем в разных соревнованиях, олимпиадах. В детстве у меня была коллекция сигарет – около 200 экземпляров. Сейчас я изготавливаю поделки для своих детей, которые посещают детский сад. И собираю на работе станки.
Биография
Евгений ВАСИЛЬЕВ родился 13 декабря 1978 года в селе Заливине Тарского района Омской области. В 1996 году окончил Заливинскую среднюю школу и поступил в ОмГТУ на механико-технологический факультет. Окончил вуз в 2001 году по специальности «Металлорежущие станки и инструменты». С 2001 года работал ассистентом на кафедре «Металлорежущие станки и инструменты». В 2003 году заочно поступил в аспирантуру и в 2005 году защитил диссертацию. В 2006 году стал доцентом кафедры «Металлорежущие станки и инструменты». С 2008 по 2011 годы работал начальником учебного управления ОмГТУ. В 2001 году вернулся в должности доцента на кафедру «Металлорежущие станки и инструменты». Женат, четверо детей.
Источник: KVnews.ru
Меню раздела