- Новости
- «К металлу надо прикасаться душой»: хроника одной плавки
«К металлу надо прикасаться душой»: хроника одной плавки
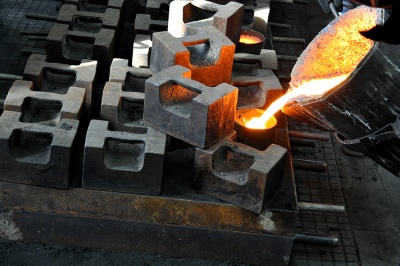
В век современных технологий, виртуальных проектов и расположенных в далекой Поднебесной производств у многих людей создается ложное впечатление о том, что окружающий мир создается легким движением мыши за экраном ноутбука и руководящими цитатами менеджеров. Но, как правильно заметил Генри Форд, при получении нового продукта все мы используем результаты труда других, лишь добавляя от себя небольшие штрихи. Увидеть рождение нового изделия и в полной мере ощутить красоту этого процесса можно на базовых производствах машиностроения – литье, штамповке, механической обработке.Сегодня мы воспользовались радушным приглашением Гарегина Сережовича Гарибяна, руководителя секции «Машины и технология литейного производства» кафедры «Машиностроение и материаловедение», посетить настоящий литейный участок (2 корпус ОмГТУ). Здесь не только идет образовательный процесс, но и активно выполняются работы по договорам с предприятиями города. Поэтому работа в учебно-производственном цехе кипит в прямом и переносном смысле.
Сразу бросается в глаза, а точнее, бьет по ушам, – это сильный шум литейки. В первые минуты пребывания в плотной, горячей атмосфере цеха чувствуешь себя чужеродным организмом: все двигаются, как слаженный механизм; кажется, что ты все время стоишь у рабочих на пути и тебе здесь нет места. Но постепенно начинаешь привыкать к ритму цеха и вспоминаешь фразу выдающегося ученого и истинного политеховца Виктора Петровича Сабурова: «К металлу надо прикасаться душой». А в голове уже крутятся отрывки из лекций по материаловедению и технологии литейного производства. Ну вот, теперь можно и выдохнуть, и ты начинаешь дышать с литейкой одним воздухом.
Материал для изготовления отливок поставляет заказчик, как правило, это лом. Сегодня мы наблюдаем за процессом отливки из лома чугуна. Если не говорить о марках чугуна, то для обывателя это выглядит достаточно тривиально. Ребята работают над заготовкой, используемой для обеспечения технологического процесса получения технического углерода при изготовлении резинотехнических изделий.
![]() |
![]() |
Способ литья определяется параметрами назначения будущей детали и ее материалом: это может быть центробежное литье, литье в кокиль или по выплавляемым моделям, спекание порошка или литье в землю. Несмотря на то, что последняя технология используется достаточно давно и точность отливок относительно небольшая, около 80% всех отливок в мире до сих пор делаются именно таким способом.
Литье ведется в опоки - специальные формы, которые сваривают сами работники в соответствии с конфигурацией изделия. В них помещается модель, затем она засыпается специальным составом из песка, глины и воды. Смесь тщательно трамбуется для того, чтобы заполнились все полости и четко сформировалась конфигурация модели. Затем модель извлекается, а образовавшаяся форма обсыпается графитной пудрой. Эта пудра служит своего рода смазкой для раскаленного металла, который будет впоследствии равномерно заполнять форму. Несмотря на оперативность и кажущуюся простоту работы, этот этап – один из самых ответственных: хорошо собранная опока может простоять перед заливкой до полугода, а вот халатности такая конструкция не прощает и может рассыпаться прямо на глазах.
![]() |
![]() |
Далее на собранную опоку устанавливают литниковую систему. Это такая горловина для заливки горячего металла. Чтобы раскаленный металл не раскрыл под давлением опоку, на нее устанавливают груз весом 200 кг. Да, это работа для настоящих мужчин. Все готово, и специалисты начинают уже колдовать с печью.
|
Температура плавления чугуна 1300 градусов по Цельсию, поэтому процесс разогрева печи и расплава металла занимает значительное время – около часа. Оператор постоянно контролирует процесс варки, внося коррективы на пульте управления, поскольку недогрев или перегрев металла приведет к браку. И работу придется начинать сначала.
![]() |
![]() |
Тем временем разливочный ковш также прогревают, чтобы предотвратить схватывание чугуна в нем при заливке форм. Чугун при варке выделяет шлак, который аккуратно убирают с поверхности, как пенку с варенья))). Металл готов, приступаем к раздаче.
![]() |
![]() |
Наверное, кипящий металл не может оставить равнодушным никого. Ощущение присутствия маленького солнца в двух шагах от тебя добавляет адреналина в кровь, и, вглядываясь в играющие потоки чугуна, с уважением думаешь о сотворении этого небольшого, но уютного мира.
![]() |
![]() |
Профессионалы не привыкли много говорить, и в короткий перекур на вопрос о работе получаю короткий ответ: «Нормально, работаем, заказы есть». Спрашиваю ребят, как они ощущают себя рядом с такой непокорной стихией, не страшно ли. Но они только улыбаются – привыкли. Работа еще не закончена: впереди процесс кристаллизации, освобождение отливок и отрезка литников.
![]() |
![]() |
Мы уходим, а парни продолжают трудовой день. Пожелаем им успешной работы, и пусть крылатая фраза советских времен "Наша сила - в наших плавках" отдает иронией, но это ирония тех, кто владеет секретами укрощения стихии металла и огня.